製品ができるまで
製品ができるまで
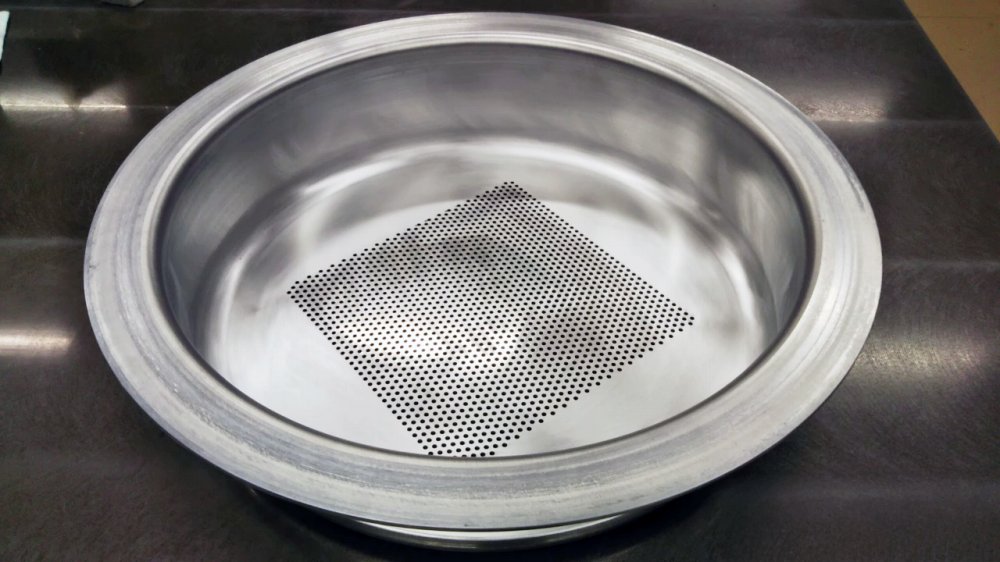
■ アルミシールド(サンプル品)ができるまで
タレットパンチプレス
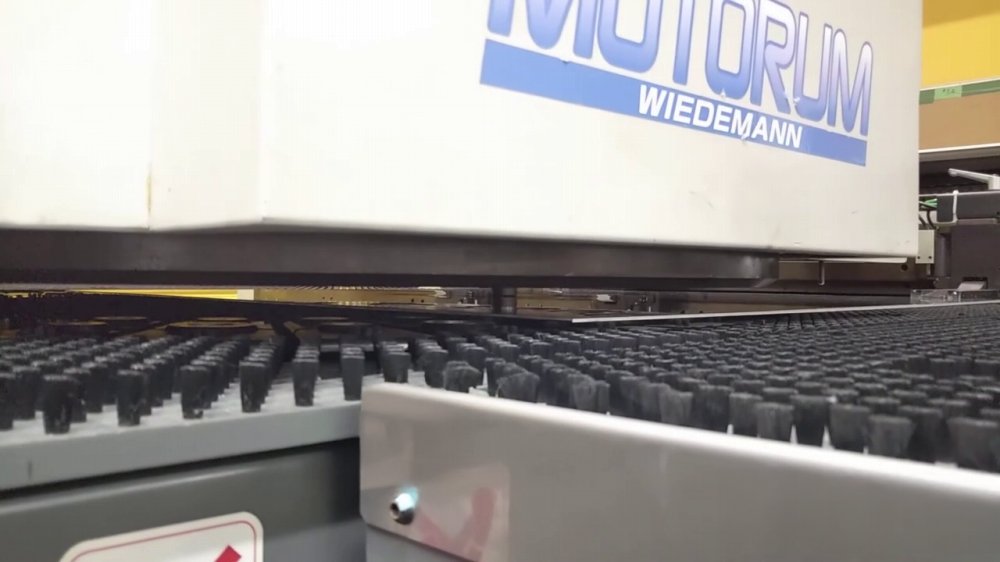
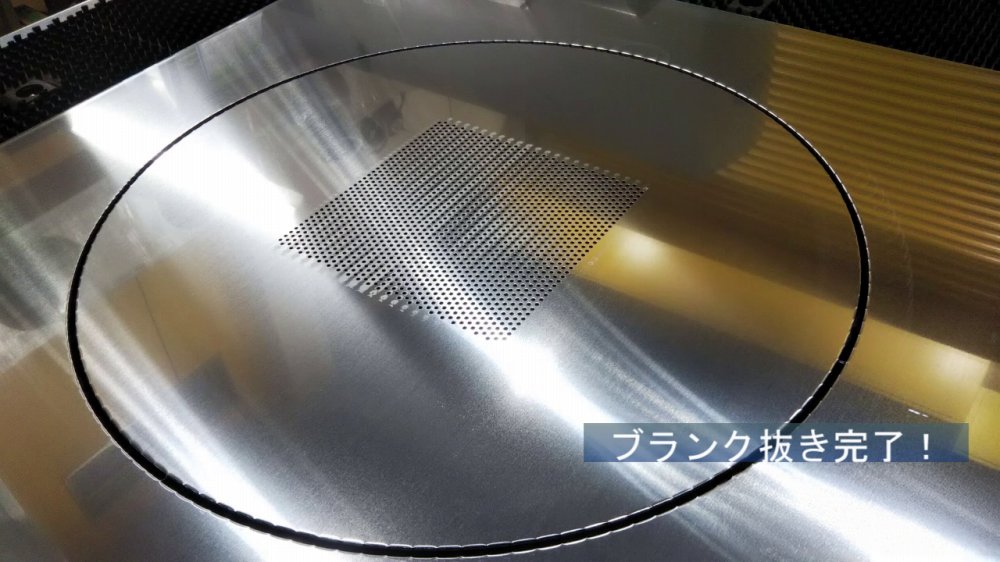
ヘラ絞り加工前に板材を加工に適した効率的な形状に切断していきます。
最終的な形状に応じて、成型加工しない箇所は事前の穴開け加工や下穴加工なども行います。
ナガセでは、タレットパンチプレスと2次元レーザ加工機の併用でブランクカットを行っており、素材の種類、形状、素材の厚みなどによって使い分け、生産性の向上を常に図っています。
ブランクカットの方法によって後工程や完成時の精度にも影響するため、各工程の作業者とも連携を取りながら最適化を図っています。
ヘラ絞り加工
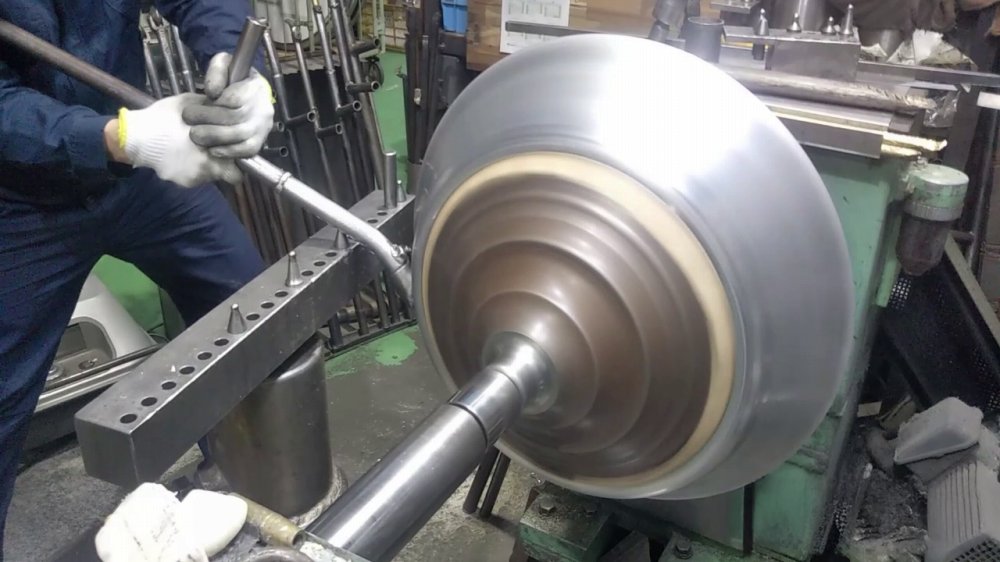
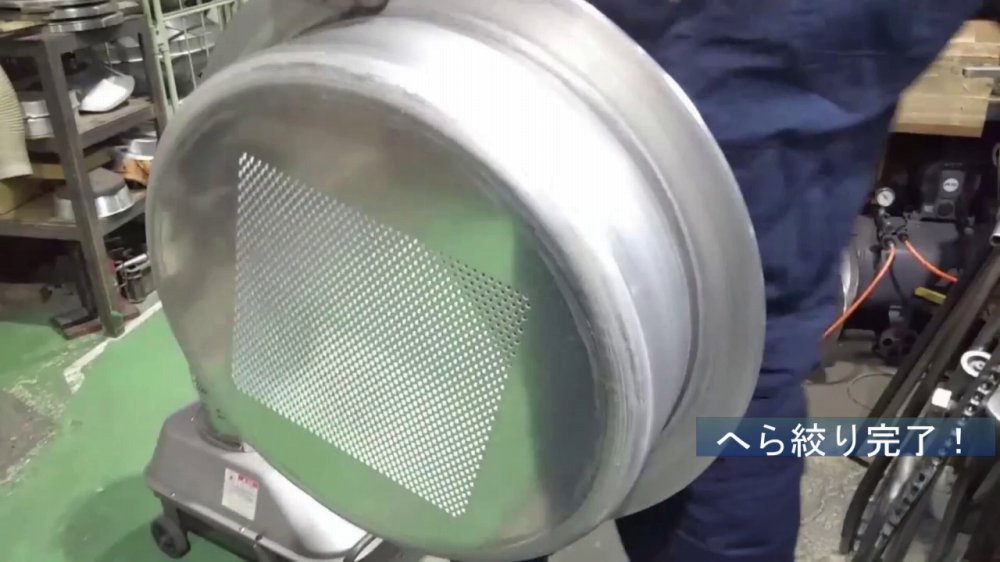
弊社のコア技術であるヘラ絞り加工でアルミの板材を成型加工していきます。
モノづくりを良く理解した上で加工しないと工業用部品としての精度や目的に応じた品質が担保出来ない為、熟練の技と積み上げてきた経験測、技術を融合させてヘラ絞り加工していきます。
ヘラ絞り加工は見た目以上に繊細で複雑な加工の為、後工程の板金溶接との兼ね合いも非常に重要です。特にヘラ絞り成型した部品と切削加工の組付け溶接はそれに特化した加工技術者でなければ工業用品として成り立ちません。
ナガセではヘラ絞りから派生した様々な加工を、他では真似できない品質レベルで実現しております。
ヘラ絞りでしか実現できないR形状や滑らかな曲面形状は、その外観と相まって非常に有益な金属加工部品として、皆様のお役に立っています。
3次元レーザ加工
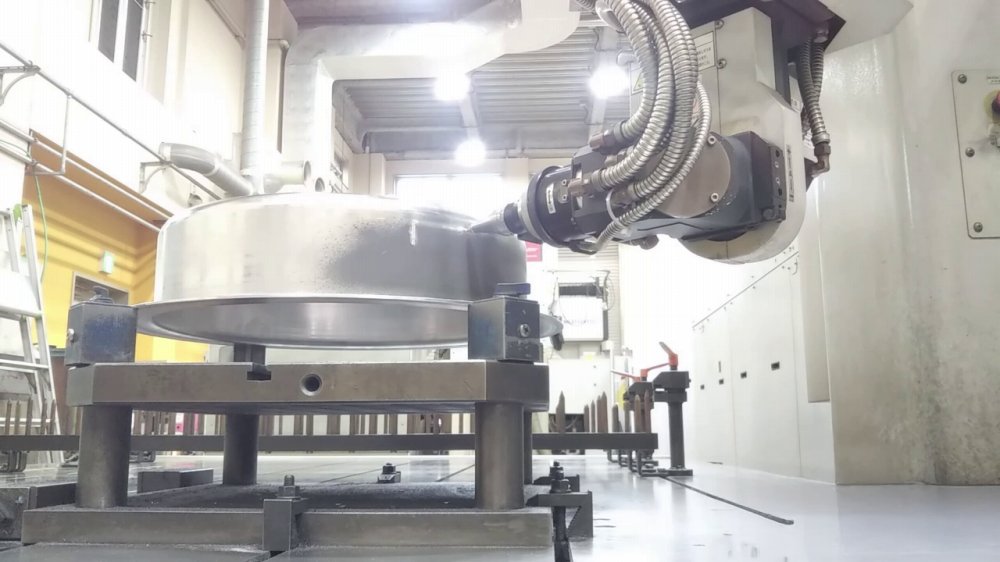
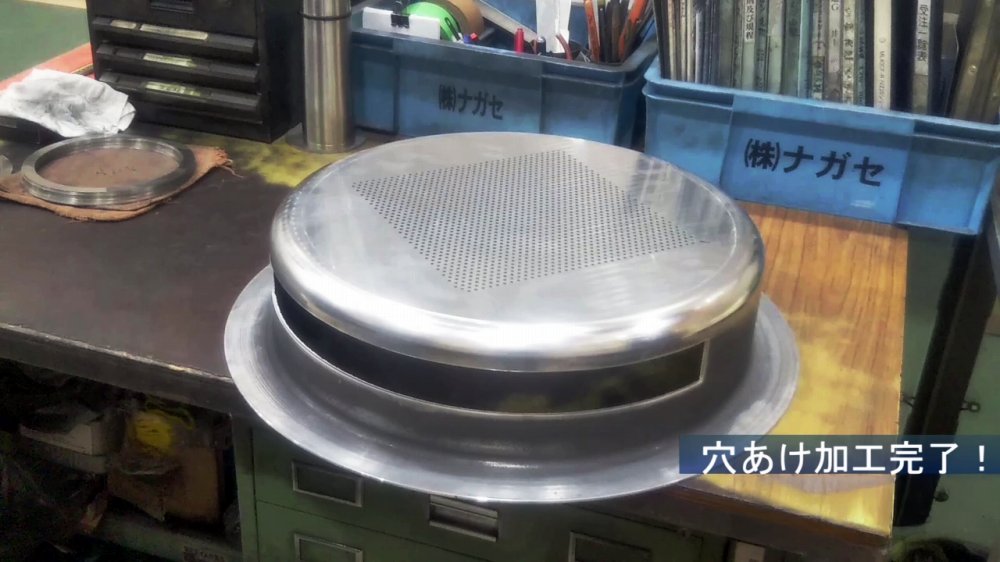
ヘラ絞り成型加工したものを、3次元的にレーザ加工していきます。
ヘラ絞り加工を終えた金属部品は、そのままで最終的な完成品になる事は少なく、レーザ加工で穴加工、切り欠きやトリミング加工していく事で、顧客要求にあった部品として完成形に近づいていきます。
ヘラ絞り成型したものを3次元的に加工するのは、ヘラ絞り加工品の扱いに手慣れた作業者でないと難しい作業であり、芯出し、位置出し等、非常に繊細な段取りが要求されます。
ナガセではヘラ絞り加工業者としては比較的早い段階から3次元レーザ加工機を導入し、その加工で実績を積んできました。精度が要求される現代の工業用金属加工部品において、付加価値と優位性を出しているのは3次元レーザ加工である、といっても過言ではありません。
バフ研磨
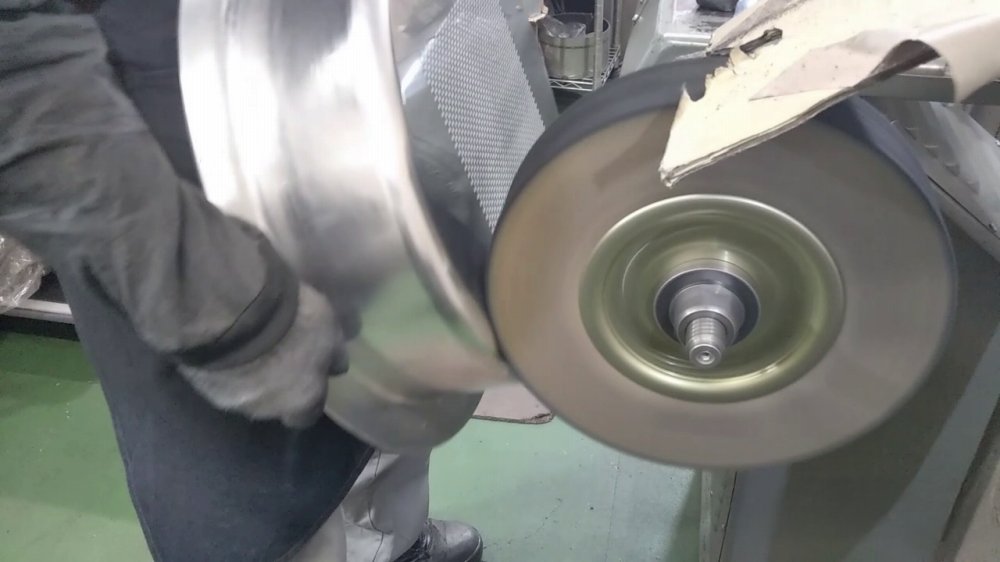
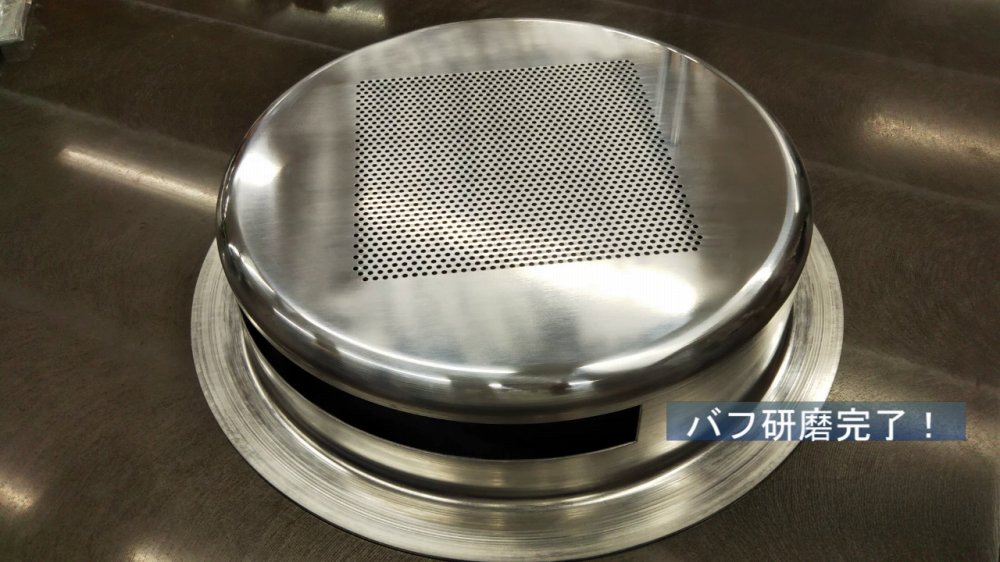
ヘラ絞り成型加工やレーザ加工を終えた後、表面をバフ研磨で整える作業です。
現代の工業用品で外観・表面がキズだらけで良い、というような物は存在しません。
どんな加工方法であっても、大なり小なり必ず加工キズや加工痕が付いてしまうものであり、その加工品の最後を人の手でひとつひとつバフ研磨していき、最終的な製品として仕上げていきます。
溶接ビード跡を平滑に仕上げたり、食品関連機器におけるキズ除去、光学機器部品における研磨加工など、その作業はありとあらゆる製品に関係してきます。
一見すると最後の工程と思いがちですが、溶接アッセンブリーしてしまうとバフ研磨出来なくなってしまう形状や製品も多々あり、そういったものは溶接アッセンブリー前の単体部品の段階でバフ研磨し、溶接アッセンブリーした後にまた最後の仕上げでバフ研磨工程を入れたりします。
ひとつの製品が出来るまでバフ研磨工程が何回も入るものも沢山あり、ナガセの品質向上、付加価値増加に繋がっています。
検査工程
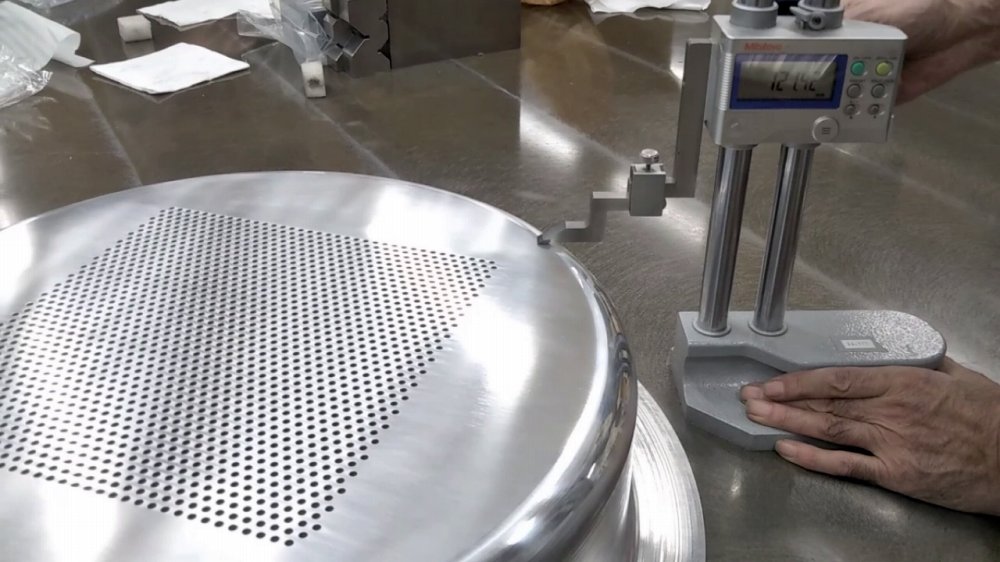
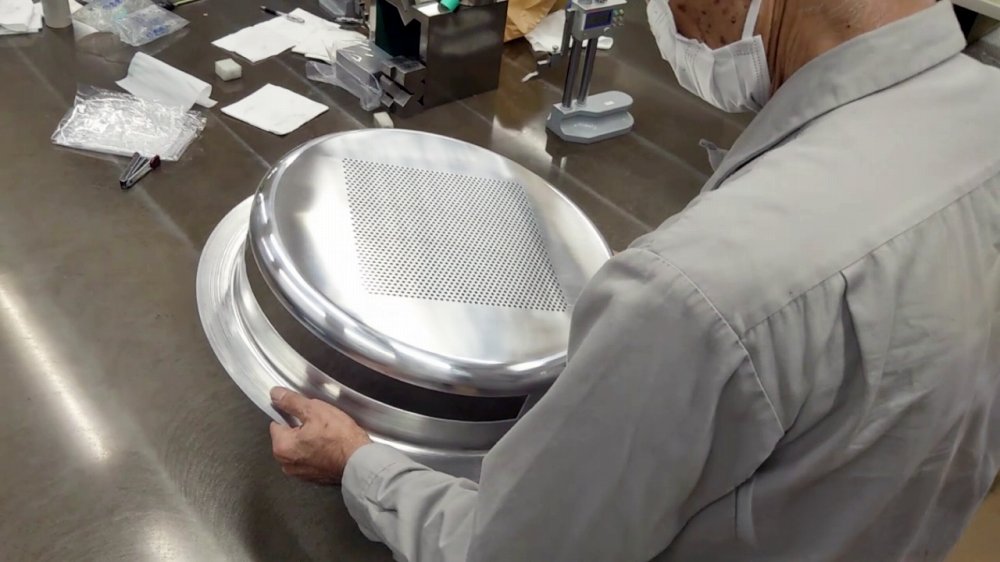
出来上がった製品に対して、要求された寸法、精度に仕上がっているかを検査し、品質を担保する工程です。
どんなに見た目が綺麗な部品であっても、その要求精度に出来上がっていなければ不良品となってしまいます。
ナガセではヘラ絞り成型加工したものを測定・検査する、というある意味非常に難しい作業を日々行っています。
一般的なノギスやハイトゲージから3次元測定器、レーザ形状測定器、キズ検知機などあらゆる測定器を使って品質の確認をし、外観検査に至るまで熟練した作業者が【ナガセ品質】を保証して皆様の元に付加価値のある高品質な製品をお届けします。
アルミシールド(サンプル品)
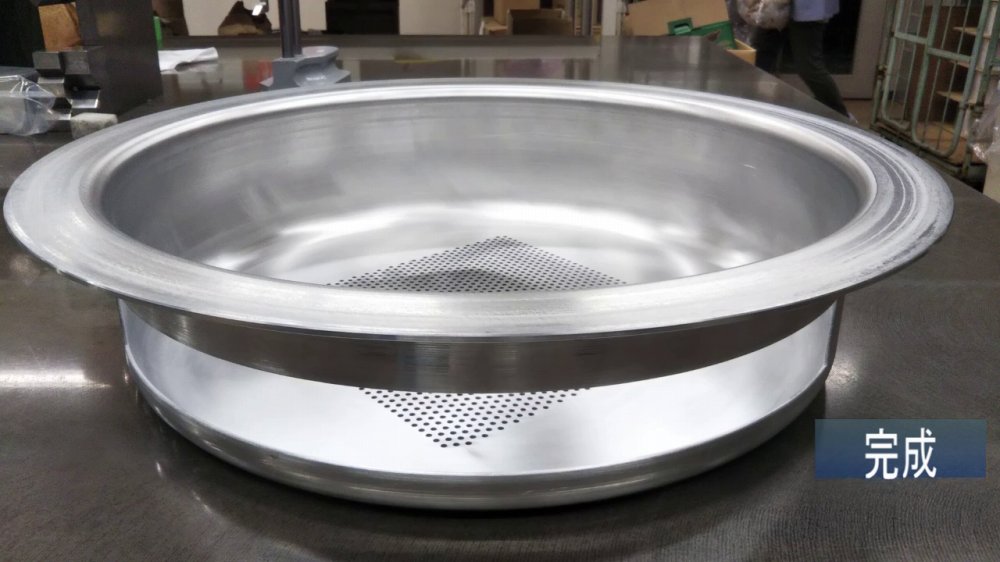
A5052の板からヘラ絞り加工~レーザ加工~バフ研磨というシンプルな工程を経て制作されたアルミ製のシールド部品。
工程自体はシンプルだが、ヘラ絞り加工でしか実現できないRや曲面、そしてフランジまでが一体で成型されています。
ヘラ絞り加工により素材が加工硬化するので、溶接での2体構造よりも強度があり、かつ軽量に加工する事が出来ます。
Rや曲面のヘラ絞り加工は、ガスの流れ、水流、空気の流れ、その他流動する対象物がある製品に対して非常に有効な加工方法であり、板金溶接加工では再現できない形状もヘラ絞り加工であれば実現する事が出来ます。
またヘラ絞りによる一体成型加工は、溶接で製作する事による歪みのリスクを抑える事ができるので幾何精度についても溶接構造より優位性を保てます。